2023.08.18
出荷検査とは?
目的や検査方法、項目をわかりやすく解説
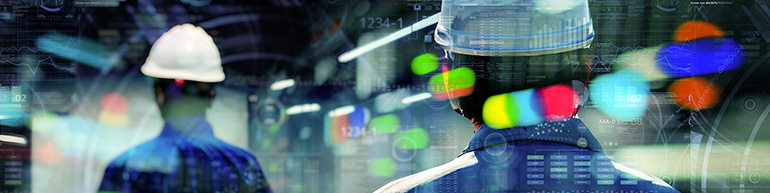
出荷検査とは、いくつかある検査工程のうちの一つで、出荷をする前に実施する検査のことです。出荷検査は取引先に製品を出荷する前の重要なポジションを担っており、出荷検査が正常に機能しなければ不良品が市場に流出してしまう可能性が高まるでしょう。そのため、出荷検査を実施している企業は、その重要性を理解したうえで取り組む環境や従業員を整備しなくてはいけません。
当記事では、出荷検査の重要性や具体的な検査方法・検査項目について解説します。出荷検査を疎かにしている企業様はないとは思いますが、確認の意味を込めて再度出荷検査について当記事を参考にしてみてください。
そもそも検査工程とは
そもそも検査工程とは、製品の外観や寸法のような機能面などを検査する工程のことを指します。どの場面に検査工程を設けるのかによって検査の名称が異なり、場面ごとに検査の内容も異なります。検査工程は、主に以下3種類があるので確認しておきましょう。
【3種類の検査工程】
- 受入検査
└外部で製造した製品を自社で受け入れる際に行う検査工程。企業ごとに、受け入れた商品の数に応じた検査数が決まっており、設定された不良率を超えると製造先に返品して再検査してもらうケースになることが多いです。 - ライン検査
└自社の製造工程内で必要となる検査工程。製品を製造した直後に外観の検査をする方法もあれば、時間ごとに製品の寸法を測って機能的に問題がないかを検査する方法もあります。基本的に、製造ラインの中で行われる検査です。 - 出荷検査
└出荷前に行う検査工程。ライン検査を入れたものであっても必ず行う検査工程で、顧客に製品を納品しても良いかの最終判断を下す検査工程となっています。
出荷検査とは
出荷検査とは、製品を出荷する前に行う検査のことで、取引先に製品を納めても問題ないのかを確認する検査工程となっています。出荷検査で漏れが発生すれば市場に不良品が流出してしまうため、製造業において出荷検査は最後の砦といえる検査工程です。
出荷検査はライン検査の延長上で行われることもあれば、数ヶ月注文の無かった製品の在庫を出荷する際などに行われることもあります。特に、プラスチック系を扱う企業の場合は、在庫品が劣化で変色するといったことも珍しくないため、在庫品を出荷する際は、検査工程を設ける場合がほとんどです。
出荷検査の目的
出荷検査は何を目的に行っているのかを知っておかないと、具体的な検査方法を明確にできません。例えば、「一つも不良を市場に流出させないための厳しい検査」を目的としているなら、全ての製品を検査しなくてはいけませんし、「最低限の機能性を維持した検査」を目的としているなら、寸法計測や勘合測定を重視した検査方法を採用する必要があります。
以下では、上記のことを踏まえつつ、出荷検査を行う根本的な目的を2つご紹介します。2つの目的を参考にしつつ、自社で出荷検査を行う目的を明確にしてみてください。
不良品の流出を防ぐ
出荷検査の一番の目的といえるのが、「不良品の流出対策」です。製造業において、取引先に不良品が流出するのは致命的なミスであり、発生した際の取引先からの信頼の低下はかなり大きなものとなります。それゆえに、製造業の多くの企業が出荷検査に力を入れており、正社員やベテラン検査員が出荷検査担当に配属される傾向にあります。
品質の維持
製品の種類にもよりますが、プラスチックのような素材の場合は、在庫として保管する期間が長くなるほど劣化します。場合によっては変色したり、割れてしまったりといったことも考えられるため、出荷検査で確認しなくてはいけません。
そこで、出荷検査を行えば、在庫保管中に不良品となってしまったものを適切に排除できるため、出荷製品の品質の維持に繋げられます。取引先に納品する製品は常に安定した品質であることが絶対条件ともいえるので、出荷検査によって品質を維持し続けることは重要な目的の一つといえるでしょう。
出荷検査の重要性
「出荷検査の目的」で、出荷検査は取引先への不良流出防止、品質の維持の観点から非常に重要な役割を持つことを説明しました。ライン工程での検査も重要な検査工程の一つですが、ライン検査だと流れの中で見逃す可能性もあるため、その不安要素を排除するためにも出荷検査は必ず必要です。
また、出荷検査は企業内から不良を流出させない役割以外にも、「取引先との信頼関係」を破綻させないといった重要な役割も担っています。不良流出が多発する企業に案件を出し続けることは、相当な関係性が無い限り難しい話です。出荷検査の重要性を理解したうえで、取引先の信頼を損ねないように努めていきましょう。
出荷までに考えられる劣化
ライン検査で良品と判断されたものでも、特定の条件下では製品の劣化を招く可能性が高まります。出荷する直前に製品の問題が無いかを確認できてこそ、製品を取引先に出荷できると判断できるため、その過程で発生する劣化等の可能性は無視できません。出荷直前までに発生する可能性のある劣化には以下の2種類があるので、確認しておきましょう。
【出荷までに考えられる劣化】
- 人的な劣化
- 経時的な劣化
上記2つの劣化の可能性を100%防げるなら問題ありませんが、基本的には不可能です。そのため、劣化の要因を知ることで適切な出荷検査を行いましょう。
人的な劣化
人的な劣化とは、主に「人が運搬をする際に発生するキズや変形」「人の手に触れやすい場所に保管することによって発生する外的損傷」などが挙げられます。つまり、ライン検査を合格した製品が、出荷に至るまでの間に人の手によって(過失)傷つけられることを指します。
不注意などから発生する破損もあれば、定期的な在庫チェックの際に誤って傷つけてしまうこともあるため、基本的には予測しにくいのが特徴です。そのため、厳重な保管がされている場合を除いて、出荷検査では必ずチェックしたい項目ですが、予測しにくい点を踏まえて検査員には慎重なチェックをしてもらう必要があります。
経時的な劣化
経時的な劣化とは、プラスチック部品の変色や鉄部品の錆などが挙げられます。経時的な劣化は、時間だけでなく保管する環境によって劣化スピードを早めることもあるため注意が必要でしょう。
ただ、人的な劣化と違って発生する劣化内容が予測しやすいため、出荷検査の難易度は比較的低いのが特徴です。例えば、錆の場合は錆にだけ注視すれば良いですし、プラスチック部品の変色は変色していないサンプル、もしくは変色傾向にあるサンプルを持ち出して比較すれば確認できます。
劣化内容が予測しやすい特徴はあるものの、万が一見逃した際は大きな信頼低下を招く可能性があるので気を付けてください。
出荷検査の方法
出荷検査を実施するにあたり、どのような検査方法があるのかを把握しておきましょう。ただ、製品ごとに発生する不良内容は異なるため、どの検査方法を採用するかは不良内容を把握・予測してから決めるようにしましょう。
【出荷検査の方法】
- 目視検査
- 寸法検査
- 梱包状態検査
- 標準サンプル品との比較検査
基本、これら4種類の検査方法は全て行われるケースが多いです。というのも、寸法にそこまで厳しくない製品だとしても規格の寸法が決まっていれば必ず一度はチェックしなくてはいけませんし、外観にそこまで厳しくない製品だとしても過度に変形・破損しているものは納品できないため、念のため検査をしなくてはいけません。必ず全てを実施する必要はありませんが、製品の特徴に合わせて最適な方法を採用しましょう。
出荷検査の検査項目
出荷検査の検査項目は、製品によって異なります。以下では一般的な検査項目をピックアップしましたが、自社で取り扱う製品の特徴に合わせて最適な検査項目を選定してください。
【出荷検査の検査項目】
- 寸法
- キズ
- 変色
- 変形
- 錆
- 梱包材の変形
- 各製品の製造過程にて発生する可能性のある不良 など
寸法や変形は特に注視したほうが良い項目となっており、これらのような不良があった場合は組み立て時に不具合を起こして、最悪の場合は他の部品もダメにしてしまう可能性が高いです。基本、どのような不良でも流出は許されませんが、「特にどの不良だと被害度が大きくなるのか」を意識しておけば、検査項目の優先順位をつけられるかもしれません。
まとめ
出荷検査とは、製品を出荷する前に行う検査のことで、取引先に製品を納めても問題ないのかを確認する検査工程です。出荷検査で見逃しがあれば、不良品が取引先へ流出して大きな損害を出してしまうだけでなく、取引先からの信頼も損ねてしまうでしょう。そのため、企業は出荷検査の重要性を理解したうえで、人材の配置等を行わなければいけません。
出荷検査の方法には目視や寸法測定などいくつかの種類がありますが、どの方法を採用するべきかについては、製品の特徴によって異なります。出荷検査を実施する企業は、対象製品にどのような不良が発生するのかを明確にしておき、それを基に適切な検査方法・検査項目の選定をしましょう。