2021.09.30
進捗の見える化や生産性向上を実現!IoT・現場帳票デジタル化事例「株式会社駒ヶ根電化様」セミナー概要
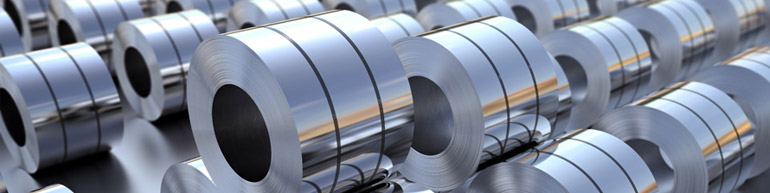
2021年2月24日、「製造現場の働き方改革 2つの事例」をテーマに、株式会社駒ヶ根電化様(メッキ処理加工)のIoT・現場帳票デジタル化事例について、オンラインセミナーを実施いたしました。このページではセミナーでお話しした内容の概要を解説しています。
セミナーの主な内容
駒ヶ根電化様では、(1)進捗の見える化ができない、(2)生産性が上がらない、(3)製造付帯業務が多い、(4)品質トレーサビリティが取りにくい、(5)洗浄水がムダに使われている、(6)設備トラブルによるチョコ停が発生、の6つの課題があり、その課題をどう解決したのか?をセミナーにて詳しくお話ししています。
現場の見える化など6つの課題
最初に、駒ヶ根電化様の6つの課題についてご紹介します。
課題1:進捗の見える化ができない
駒ヶ根電化様は、ハンディターミナルを用いて、作業の進捗状況を入力されています。しかし、進捗に応じて都度入力することができておらず、「後付けで、仕事が終わってから入力する」、「入力を忘れてしまう」ことが頻繁に発生していました。そのため、リアルタイムの進捗確認ができない状態でした。
例えば、お客様から「明日持ってきてくれないか」など、「特急の仕事」が入ると、進捗の見える化できていないことの影響が大きく出ます。その仕事が本当に今日の出荷に間に合うのか、いつ終わるのかわからないからです。その結果、技術者・管理者が、現場に出向き、進捗を確認しにいかなければならず、本来の業務が滞ってしまいました。
課題2:生産性が上がらない
駒ヶ根電化様の仕事の量は、日によって波があるそうです。そのため、仕事量が少ない日は、仕事をゆっくり進めても出荷に影響がでません。ですが、もし、忙しい日と同様に密に仕事を進めることができれば、空き時間を作ることができ、その空いた時間を違うことに使えます。仕事を進める速さの実力を知ったり、工数集計のために、何時から何時まで何の仕事をしたのかという作業日報を記録していますが、実績のサイクルタイムがわかるような正確な時刻が記載されてはいません。その結果、「本当にそれだけ時間がかかるものなのか」や「チョコ停が発生して作業が中断した」ような実態がなかなか分からないといった課題が発生していました。
課題3:製造付帯業務が多い
製造現場では様々な「紙」があります。稼働や品質管理の日報・週報・月報、あるいは現場の設備の点検記録、清掃記録などです。これらの紙は、当然手書きで書かれていますから、紙を回収・集計してエクセルに入力する業務には大きな手間とリードタイムがかかっていました。本当にやりたいことは、データを作ることではなく、そのデータを使って、現状を分析し、改善に活かすことのはずです。しかし、このような本来の仕事ではない仕事が非常に多いと、それだけで疲れてしまい、それで仕事が終わった気になり、本来やるべきことに時間を使えなくなっていました。
課題4:品質トレーサビリティが取りにくい
メッキ処理加工の品質は、「その時の設備の状態、電流・電圧・液温・液濃度」などでコントロールされており、それらのデータは設備を制御するPLCに残されています。しかし、そのデータは製造ロットと紐付けては残されていません。また、そのロットに対して「検査結果がどうだったのか」は紙で記録していました。
このため、何か問題が発生した時、それが作られた製造ロットを特定し、そのロットがいつ設備を流れたか、作業者は誰だったのか、そのときの設備にトラブルはあったのか、さらに、そのロットの検査結果はどうだったか、かなどを、何時間もかかって、紙の情報やPLCの情報から紐づけるのが非常に大変でした。製造ロット単位で全ての情報を紐づけるにはどうすればいいか?それがどうやって作られたのかという「生い立ち」をカルテのように整理して、簡単に取り出すこと、これが大きな課題となっていました。
課題5:洗浄水がムダに使われている
メッキ処理加工特有かもしれませんが、洗浄水が無駄に使われているという課題がありました。メッキ処理では、必ず化学薬品を使いますので、それぞれの工程終了後に水で洗浄すると、洗浄水に薬品が混ざります。薬品の混ざった水をそのまま下水に流すわけにはいけませんので、廃液処理をしなければなりません。
この廃液処理コストが年間2000万円ぐらいかかっており、洗浄水を使えば使うほど、廃液処理コストが高くなります。このため、洗浄水の量をコントロールしなければならないのですが、不要な時も洗浄水を流しっぱなしにしているといったことが度々発生していました。洗浄水のバルブの自動制御など、コスト削減を実現する仕組みが必要となっていました。
課題6:設備トラブルによるチョコ停が発生
駒ヶ根電化様では、設備のトラブルが発生すると、発生してから修理するという、BM(Breakdown Maintenance)で対応されています。しかし、チョコ停というほんの数分レベルの停止であると、いちいち製造日報にチョコ停を記録しないこともありました。この結果、設備トラブルによる稼働停止の実態が正しくわからない状態でした。めっき業は、装置産業のため、設備稼働率が大事なのですが、その稼働率を正確には把握できていませんでした。さらには、壊れてから対応するのではなくて、壊れる前に適切なタイミングで設備を保全できないか?予兆保全できないか?といった課題をお持ちでした。
6つの課題を解決するための具体策「工程の見える化システム」
6つの課題を解決するために導入されたのが上記の「工程見える化システム」です。簡単に課題解決のポイントをご紹介します。
課題1、2に対する解決策
ハンディターミナルで入力をしないと設備がスタートしない、などの工夫により、「後付け入力」や「入力忘れ」を確実に防ぎ、進捗とサイクルタイム(CT)が正確に把握できるようになりました。これによりCTのバラつきも見えるようになりました(下図AB)。
課題3に対する解決策
タブレットで検査結果を入力し、製造ロットと即座に紐付けることで、Xbar-R管理図などをリアルタイム自動で作成されるようになりました(下図C)。
課題4に対する解決策
基幹システムの受注Noと製造LotNoを紐付けして、生産スタート時にPLCに渡すことで、 PLCの設備制御実績データを出荷ロットに紐付けて、管理できるようになりました。PLCのデータは、数日間で上書きされていましたが、全てデータベースに蓄積されますので、お客様からの問い合わせ時に即座に関連するデータを確認すすることができるようになりました(下図DE)。同時に、設備稼働率などの管理帳票集計も自動で作成されます(下図C)。
課題5に対する解決策
洗浄水のバルブに、水量センサー付き制御バルブを導入し、PLCでコントロールすることで、洗浄水のムダな利用が抑制されました(下図F)
課題6に対する解決策
今まで、人が参照していなかったPLCログのエラー情報を収集、監視することで、予兆保全できるという仮説を立てています。たとえば、「5号機チャックNG」というエラーがPLCから出力されることがあります。これは何らかの原因で、5号機がチャックミス(掴み損ね)をしたという情報ですが、このとき、PLCはリトライをかけるようにプログラミングされています。リトライの結果、OKになれば、そのまま設備は何事もなかったかのように動作を続け、人間は気づきません。また別のタイミングで、同じエラーが出たとき、リトライしてもまたNGになる場合があります。2度目のリトライをかけたときOKになったとします。そんな状況を繰り返し、たとえば5回リトライしてNGなら、PLCがそれ以上のリトライを諦めて、設備が故障したとして、停止させるというようなプログラムになっているとします。そんな場合は、NG回数の推移を監視することで、予兆保全が可能になるケースがあります(下図E)。
<工程見える化システムの概要図>
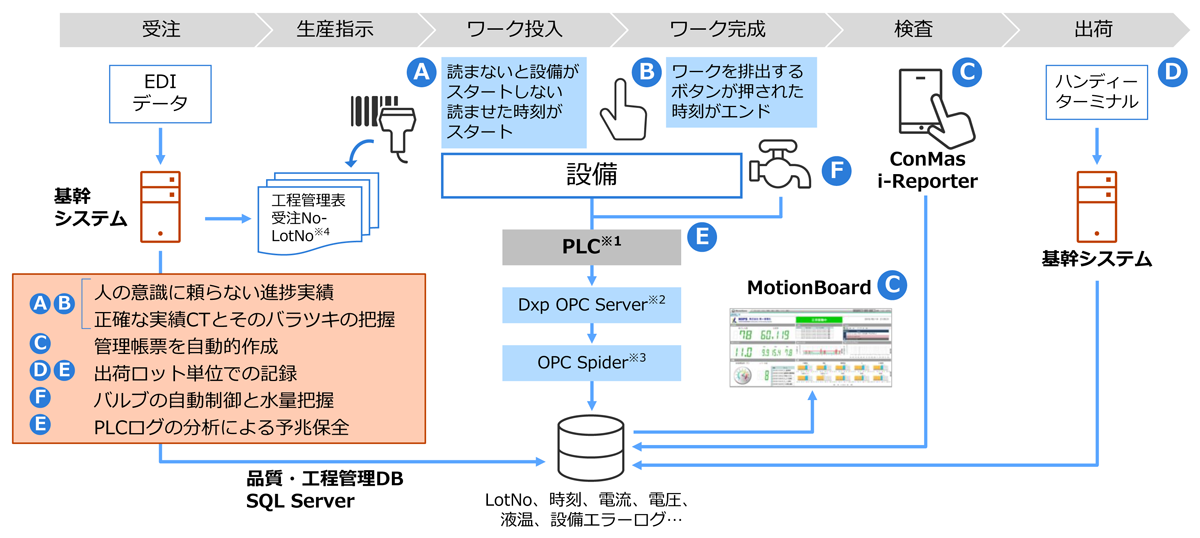
上記のような工夫を行い、下記のようなモニターで見える化を実現しました。
<工程見える化システム~トップ画面>
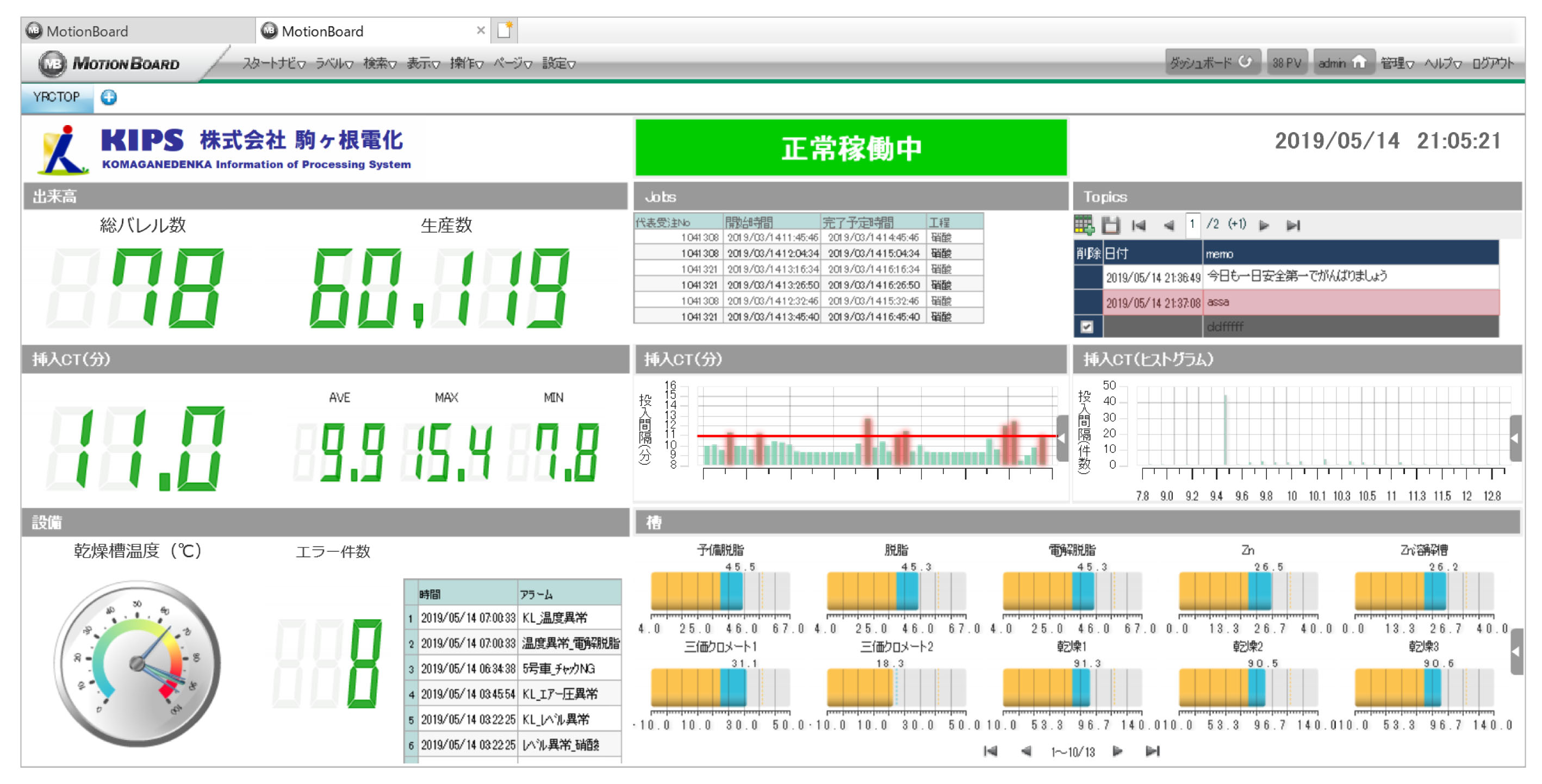
これにより、主に下記のような成果を得ています。
- 作業実態をデータで把握することに成功
- ガントチャートで生産実績を見える化
- 設備稼働率の自動集計
- めっき膜厚 X-R管理図の自動作成
- 水量自動制御と使用水量の推移の見える化
- 設備点検結果「タブレットで入力した結果を自動表示・見える化」