Based on Fujifilm’s outstanding history in organic chemistry, thin-film coating and manufacturing excellence, we have developed a highly functional membrane element. Fujifilm Apura™ has proven itself for treatment of natural gas and distinguishes itself with resistance against contaminants like aromatics and water.
Gas Separation Membrane Equipment
Fujifilm offers spiral wound membrane elements for selective gas separation. These membrane elements contain semi-permeable polymeric membranes. Separation is based on the difference in permeation speed between different gasses. The driving force for permeation is the partial pressure difference across the membrane. Fujifilm membranes enable high permeation and permeation differences between gasses resulting in high permeation rates and high selectivity. Furthermore, Fujifilm’s unique polymer type and multi-layer structure ensure high durability and stability.
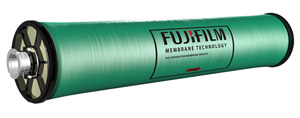
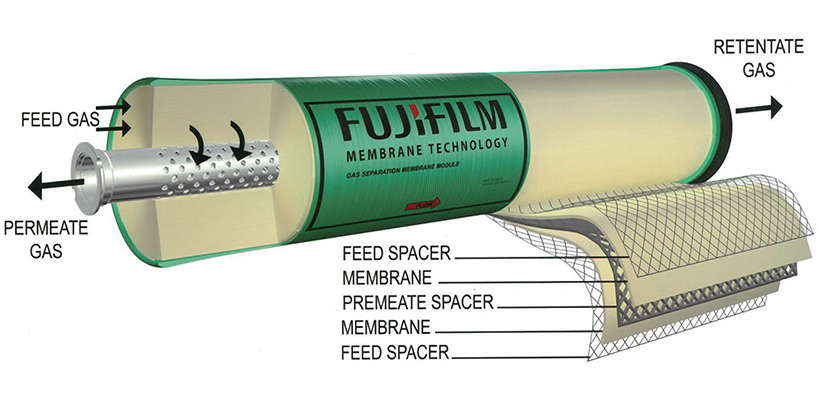
Apura™: Gas Separation Membrane Element for Natural Gas Sweetening
With Fujifilm’s new gas separation element Apura™, our clients are able to sweeten their natural gas in an efficient and cost-effective manner. The elements can be used for bulk and fine removal of acid gas in natural gas processes.
Apura™ gas separation membrane includes two products- Apura™-1.5XF and Apura™-2.0C, which are designed to maximize the CO2 removal capacity (Apura™-1.5XF) and Hydrocarbon recovery (Apura™-2.0C).
These membranes can be combined in stages to be able to maximize the overall separation efficiency.
Function of Apura™
Under the influence of partial pressure, Fujifilm’s spiral wound membrane elements (modules) remove CO2, H2S, and water from a natural gas feed stream. This membrane separation process results in an enhanced caloric product stream (also known as residue) that is low on CO2, H2S, and water and in a waste stream that is lean in hydrocarbons and rich in CO2, H2S, and water.
Innovative technology
Using our proprietary technology, we offer highly functional and cost-effective gas sweetening membrane elements with high CO2 / hydrocarbon selectivity, resulting in lower CAPEX and OPEX for our clients. Fujifilm utilizes multilayer composite membranes, which makes the modules extremely robust toward aromatics and water.
Fujifilm Apura™ has been proven in different worldwide installations, including full replacements of conventional gas separation sites, which leads to a reduction of CO2 emissions.
Customized modules
Fujifilm’s membrane elements fit in the regular 8- and 8¼-inch pressure vessels.
Apura™-FG: Gas Separation Membrane Element for Fuel Gas Conditioning
With Fujifilm’s new gas separation element Apura™-FG, our clients are able to condition their natural gas stream in an efficient and cost-effective manner. The elements can be used for heavy hydrocarbon (Ethanes+) and bulk H2S removal in fuel gas conditioning processes.
Function of Apura™-FG
Under the influence of pressure, Fujifilm’s spiral wound membrane elements (modules) remove heavy hydrocarbons and H2S from a natural gas feed stream. This membrane separation process results in a reduced caloric product stream (also known as fuel gas) that is low on high hydrocarbons and H2S and in a waste stream that is rich in hydrocarbons and H2S.
Applications of Apura™-FG include Wellhead Natural Gas Conditioning, Fuel Gas Conditioning for Gas Engine, and Gas Turbine.
Innovative technology
Using our proprietary technology, we offer highly functional and cost-effective fuel gas conditioning elements with high hydrocarbon (Ethanes+) selectivity towards methane, resulting in more efficient plant operation and reduced Volatile Organic Compounds (VOC) emissions which result from the combustion of heavy hydrocarbons.
Fujifilm utilizes multilayer composite membranes, which makes the modules extremely robust toward aromatics and water.
Customized modules
Fujifilm’s membrane elements fit in the regular 8- and 8¼-inch pressure vessels.
What are Gas Separation Membranes?
Gas separation membrane technologies describe techniques for separating gasses. Gas separation occurs by feeding a pressurized gas into a membrane module. Implementing gas separation solutions divides or purifies single or multiple gas components. The membrane is typically a non-porous polymer layer, and it's possible to execute selective gas separation by tuning the permeability of selected species by specific material design.
Polymeric membranes are the preferred choice in natural gas applications because of their excellent CO2 removal capacity. The most effective gas separation membranes combine exceptional permeability with high selectivity.
The solubility and diffusivity of each component dictates the separation through the membrane. This gas separation process begins with dissolving the particles onto the membrane and diffusing through the film at different rates.
Advantages of Membrane Technology Over Amine
Amine (aqueous alkanolamine solution) technologies offer another gas treating and CO2 removal method by feeding crude natural gas to a specially designed unit including an absorber and a regenerator.
The acidic CO2 molecules bond with the amine solution to create a dissolved salt material in the absorber unit. The purified gas then flows out of a product valve while the amine solution flows into an exchanger for cleaning and regeneration with heating in the regenerator unit.
Amine technologies can reach up to low parts-per-million specs for both CO2 and H2S.
A significant difference between the two gas separation solutions - amines and membranes - is that amines technologies require the contaminants to undergo a chemical change while membranes allow the molecular structure to remain intact.
Membrane gas separation processes offer several advantages over amine gas treatment alternatives:
- Reduced operator demand: The gas separation equipment and technologies used with membranes are less complex than amine, resulting in simplified operations. No moving parts means fewer maintenance requirements.
- Lower CAPEX and OPEX: Your capital and operating expenditures will be lower when utilizing gas separation solutions.
- Reduced energy consumption: Gas contaminant removal via membrane technology requires less power than amine, thus reducing utility costs.
- Eco-friendly: Gas separation membranes reduce your carbon footprint by 40% to 60%, require no hazardous chemicals and produce lower CO2 emissions, making it a more environmentally friendly solution.
- Simple installation: Membrane technologies feature a modular design, which simplifies the installation process. You can have your gas separation equipment up and running faster and at a lower cost.
Fujifilm Can Help With Your Gas Separation Needs
Fujifilm has the experience and knowledge to assist with every aspect of the gas separation process. Whether you're an oilfield equipment and service company looking to build a new plant or an oil and gas operation seeking to upgrade existing membrane technology, our specialized team can provide expert guidance every step of the way.